Clear Advantage:
Transparent Barrier Film has the Flexibility
to Flourish
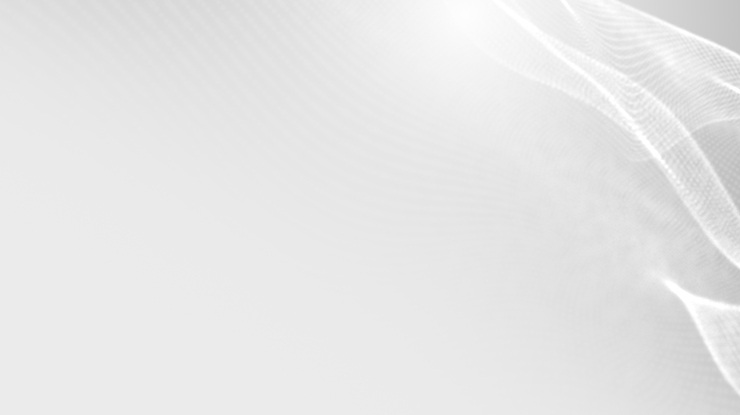
As consumer goods companies seek more sustainable forms of packaging, TOPPAN’s proprietary GL BARRIER film is making strides in the global marketplace.
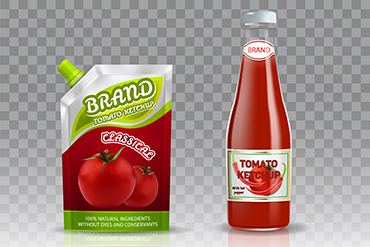
One recent trend that’s immediately obvious upon visiting a supermarket or convenience store is the big shift from rigid to flexible packaging. Foods that were traditionally sold in glass jars or metal cans—think tomato purée, honey or potato salad—and toiletries that were sold in bottles—liquid soap, for example—are now available in glossy pouches in a whole range of shapes. According to market research company Euromonitor International, flexible packaging accounted for over 40% of total packaging globally in 2019, and over 50% of food product packaging.
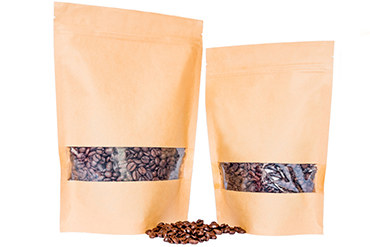
What’s driving this shift? The primary factor is so-called lightweighting. Cans and bottles are heavy and bulky and produce more carbon dioxide—a greenhouse gas—when transported, while glass is prone to break. By contrast, flexible packaging is lighter, less bulky and more eco-friendly in transit. All these are major positives.
Flexible packaging is not, however, monolithic. There are different kinds: flexible packaging made with aluminum foil and flexible packaging made with other materials. Aluminum foil has excellent barrier performance that other materials can struggle to match. Now, though, barrier film is making serious inroads. Why? First, the fact that film is transparent is a big plus. It enables producers to display food products in the most direct, mouth-watering way possible, while providing reassurance to consumers purchasing things like baby food, where safety is a priority. Non-metallic packaging has other safety advantages: it can be passed through metal detectors for protection against food tampering. It is also microwaveable, something that time-constrained consumers value particularly highly.
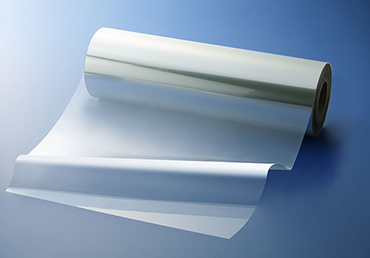
TOPPAN saw the potential of barrier film early. It started producing GL BARRIER, its proprietary family of vapor-deposited barrier films, in 1986. GL BARRIER’s most crucial advantage is this: it performs the essential task of protecting package contents from moisture and oxygen to a similar standard to aluminum, delivering long shelf life and reduced food loss, something that few other aluminum foil alternatives have yet achieved.
International expansion
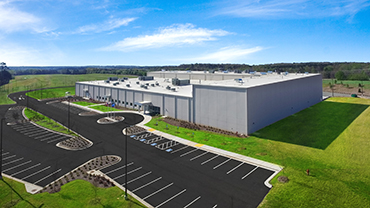
For the first three decades of GL BARRIER’s life, TOPPAN served the global market from two plants in Japan. However, as demand for GL BARRIER increased, major producers of fast-moving consumer goods and packaging manufacturers in the United States, Europe and Central and South America started to require shorter lead times and enhanced levels of service.
TOPPAN responded by launching the construction of a roughly US$100 million GL BARRIER production plant in Griffin, Georgia, in 2014, following that by the opening of a dedicated sales office in Chicago in 2015. The almost 104,000-square-foot factory, which boosted TOPPAN’s production capacity by 40%, started operations in April 2016.
The Georgia plant, which currently employs 80 people, serves the North American, European, and Central and South American markets. Thanks to its location, it can offer shorter lead times, local product development, technical assistance and stability of supply.
Mono-material: the key to recycling plastic packaging?
At the same time as expanding GL BARRIER’s geographical reach, TOPPAN is also working to reinforce the brand’s environmental credentials.
While GL BARRIER has a number of intrinsic environmental advantages compared to aluminum—the production process is less energy-intensive and CO2-generative, while film does not generate hazardous chlorine gas when incinerated—ideally, the discussion should move onto a different plane.
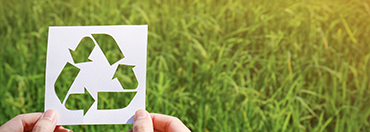
As explained earlier, TOPPAN supplies its GL BARRIER film to packaging manufacturers (converters) who make the final product packages for brand owners. Traditionally, the converters have combined GL BARRIER film with other elements in a laminated package made of different kinds of materials.
But packages made of multiple materials like this present a challenge to recycling centers, which are typically set up to process a single material—paper, metal, glass or a specific plastic—in dedicated streams. Separating laminated materials is difficult, while putting a multi-material package through a dedicated recycling stream will taint the output.
Mono-material packaging is the solution.
Next-generation packaging materials
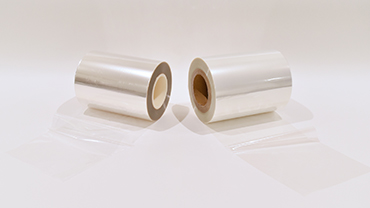
TOPPAN has stepped up to the plate, unveiling a full range of transparent barrier films for functional mono-material packaging based on the three most common plastics, polyethylene terephthalate (PET), polypropylene (PP) and polyethylene (PE).
Thanks to TOPPAN’s breakthrough solutions, converters can now match the GL BARRIER film materials with the materials in the other layers to create a mono-material package. On top of the direct environmental benefits, using more readily recyclable packaging enables brands to build loyalty by proving their commitment to environmental responsibility to consumers, especially young consumers.
With a world-leading 40% market share in its category, GL BARRIER film is currently used in 15,000 products in 45 countries and regions, in industries ranging from food and beverages and health and beauty to medical and electronics. As the focus on sustainability intensifies, more companies are likely to reach for this innovative, lightweight and eco-friendly packaging option.
Toward a sustainable society
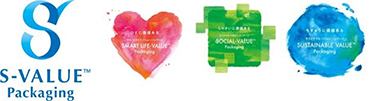
The need to tackle environmental issues, such as climate change and marine plastic waste, and the rapid advance of digitalization prompted by the COVID-19 pandemic are bringing about significant shifts in economic activity and people’s lives. GL BARRIER is part of “TOPPAN S-VALUE Packaging,” a new brand designed to drive business based on a vision of packaging that offers value and contributes to a sustainable society and fulfilling, comfortable living.