SocialEmployee Health & Safety / Work-Life Balance
Basic ApproachBack to Top
TOPPAN values Group employees as precious “human assets” and understands how deeply it depends on them. Mindful that human assets excel most when they are vigorous, earnest, and driven, TOPPAN Holdings Inc., the Toppan Printing Labour Union (“the labor union”), and the TOPPAN Group Health Insurance Union (“the health insurance union”) promote rewarding working conditions and healthcare and safety initiatives to support motivated, vigorous, and earnest work. For employee health and safety, we undertake various activities based on the Health Management Declaration (est. in 2015, revised in 2019) and the Basic Policy on Safety, Health, and Fire Protection (updated in April 2020 from the Basic Policy on Health and Safety est. in 2010). The declaration clarifies health management policies for maintaining and enhancing the health of Group employees. Based on data visualizations that track “health and productivity management®*,” this declaration reorganizes health promotion measures and action plans implemented by the Group and the health insurance union. Two aims are pursued: further promote the health of employees and their families through various approaches such as supporting work-life balance, and contribute to society through healthcare businesses that support community health. The Basic Policy on Safety, Health, and Fire Protection, meanwhile, enunciates a “safety first” principle as a top priority for the entire workforce, including both regular and contract employees, towards the complete elimination of occupational accidents. Our efforts to eliminate occupational accidents are constant.
- *
- Registered trademark of the Workshop for the Management of Health on Company and Employee of Japan
Promotion FrameworkBack to Top
The Personnel & Labor Relations Division coordinates with general affairs departments at Group sites to implement various measures on labor matters in consultation with the labor union. The division also spearheads the development of employee healthcare and safety initiatives in cooperation with the labor union, the health insurance union, and general affairs departments at operational sites throughout the Group.
Organizational Framework for Health Management Promotion
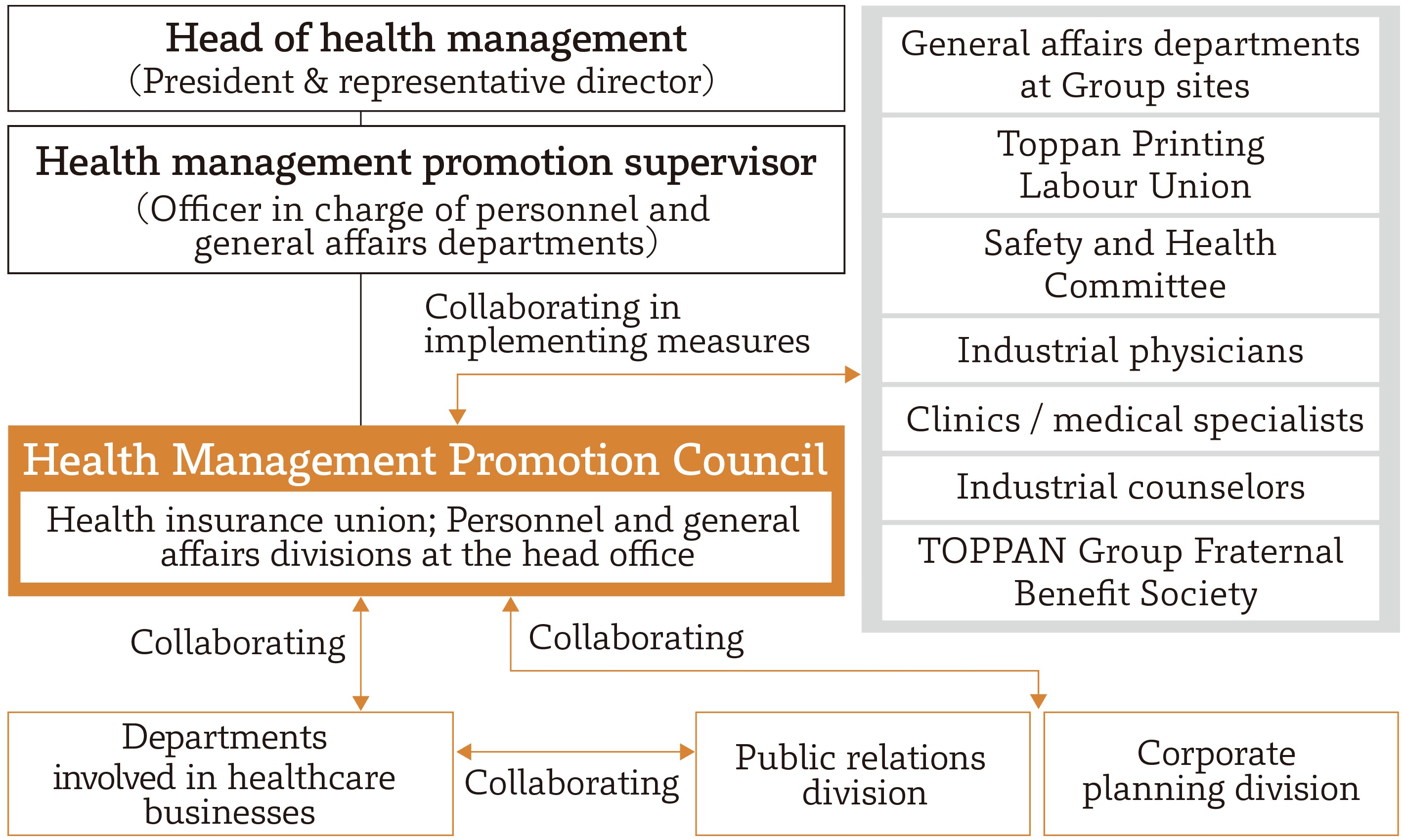
Labor-Management Partnership at TOPPAN Inc.
The labor union and management at TOPPAN Inc. collaborate on various issues on an equal footing as partners that share and respect each other’s ideals. Business councils are convened as cross-divisional and operational-site-based forums to discuss wide-ranging managerial issues. Several special committees are convened to deliberate pertinent issues. Standing committees also meet to discuss issues such as working hour reductions, wages, and safety and health. Individual labor-management committees meet whenever necessary to discuss designated subjects such as the creation of a working environment amenable to enhanced job satisfaction. TOPPAN Inc. has adopted a union shop system. In principle, all non-managerial employees belong to the labor union.
Health Management
A Health Management Promotion Council at TOPPAN Holdings Inc. has developed a framework for promoting “health and productivity management®.” The president & representative director oversees the council as the head of health management. Groupwide representatives meet with the health insurance union to establish key targets and key performance indicator (KPI) benchmarks for employee health initiatives. The council members discuss, implement, verify, and improve various healthcare measures to achieve the targets and benchmarks.
Investment for Health Management
Fiscal 2023 | |
---|---|
Clinic operation cost (covered by the company) |
Approx. 250 million yen |
Occupational Safety and HealthBack to Top
Safety masters, safety personnel, employees in charge of engineering and safety, and other safety experts have been deployed to operational sites across Japan under the safety promotion framework of the Group. TOPPAN organizes comprehensive safety training for all Group employees, both regular and contract hires, in accordance with the Basic Policy on Safety, Health, and Fire Protection. The training takes many forms, from safety programs mainly for forepersons to risk assessment courses to enhance the intrinsic safety of machines and equipment.
Anzen Dojo
Anzen Dojo safety-training facilities outfitted to simulate and alert employees to workplace hazards have been operated at three domestic sites for over a decade: the Kawaguchi Plant (Saitama), Takino Plant (Hyogo), and Fukuoka Plant. Two newer dojos opened at the Gunma Central Plant and Shiga Plant in Japan, respectively, in fiscal 2020 and 2021. Overseas, dojo facilities were set up at Group sites in China and Thailand in fiscal 2017. TOPPAN will continue upgrading Groupwide safety promotion activities to prevent occupational accidents, with support from the five domestic dojos and two dojos overseas. External companies and organizations come to train at the dojo facilities in Japan. While most train at the Kawaguchi dojo, inquiries on their use are welcome at the other plants. The Kawaguchi dojo is equipped with a virtual reality (VR) simulator to train employees and guests on the handling of workplace hazards. This dojo also uses mechanical simulators to familiarize trainees with the dangers of dust explosions and hazardous chemical exposure.
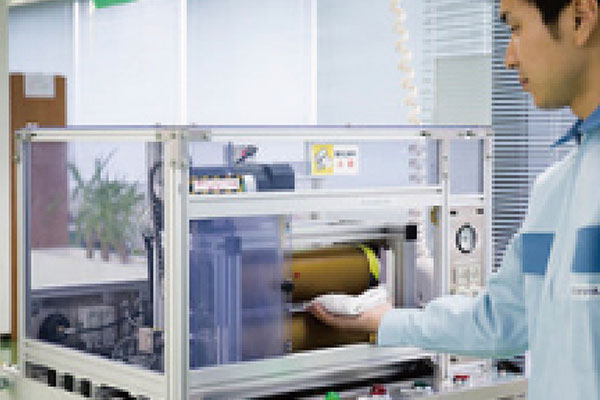
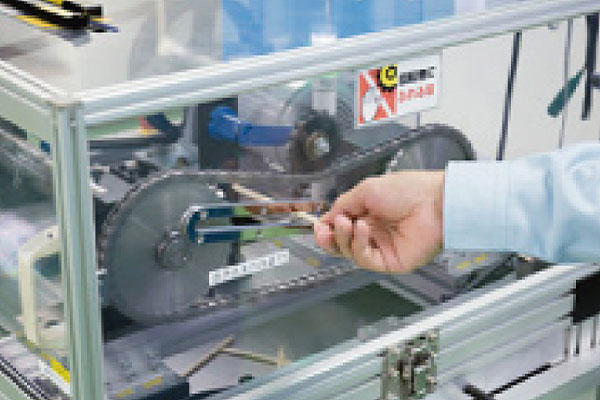
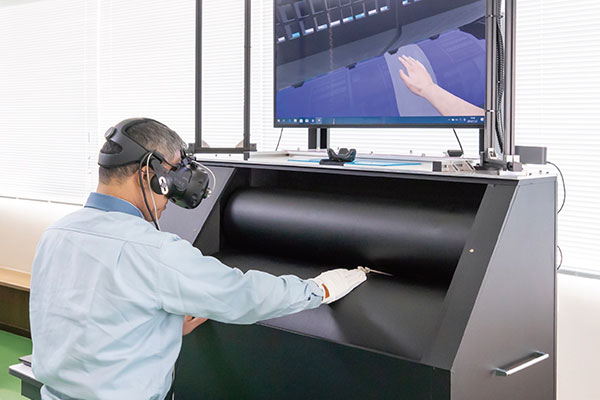
Operating Anzen Anzen Dojo Overseas
Dojo facilities were opened at Siam Toppan Packaging (Thailand) in October 2017 and the Toppan Leefung Dongguan Plant (China) in January 2018. Both facilities leverage expertise on safety training cultivated at the domestic dojos and are equipped with safety-related displays and hazard simulators optimally selected for the working conditions at their sites. TOPPAN fosters onsite safety masters for overseas Group companies and regularly holds safety sessions for frontline operators according to the operational scheme applied in Japan. Anzen Dojo tours with hazard simulators were conducted to ensure employee awareness of potential workplace dangers at four Group sites in the U.S. (May 2019), two sites operated by Giantplus Technology Co., Ltd. (November 2019), and several Group sites in Indonesia and Thailand (May 2020).
On a cumulative basis, 39,968 Group employees and visitors from around the world have taken safety training since the first dojo opened in fiscal 2010. Trainees from external companies and organizations have been limited to about 200 per year since fiscal 2020, mainly due to temporary site closures during the COVID-19 pandemic. Notwithstanding the four-year slowdown, a cumulative total of 7,557 visitors from 1,040 entities have trained at dojo facilities. TOPPAN has also been using VR technologies to produce hazard simulation content since 2019. In total, 22,678 Group employees have been trained on workplace hazards in Anzen Dojo VR tours organized at 55 operational sites across Japan. The innovations at the dojos for remote hazard training during the pandemic have heightened safety awareness across the Group.
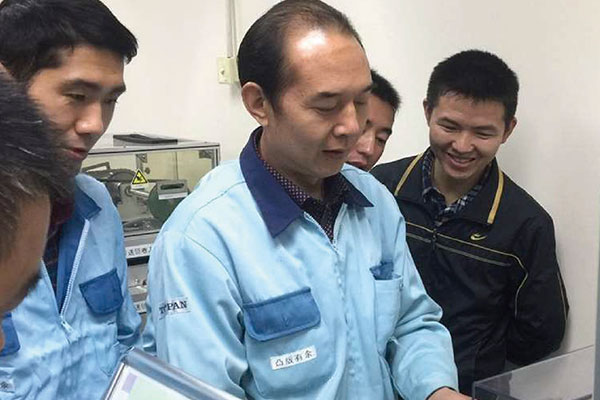
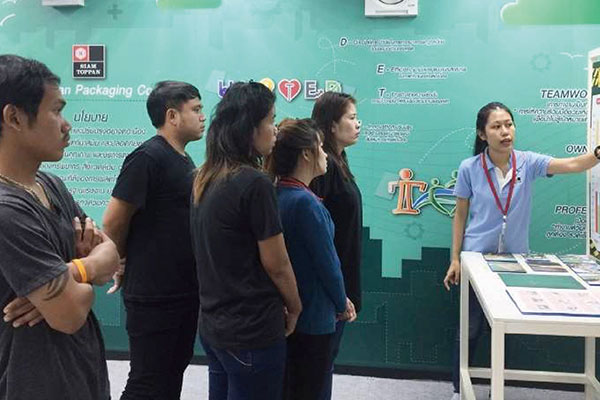
Anzen Dojo Opened
Domestic Group Sites
- Fiscal 2010
- Kawaguchi Plant (Kawaguchi, Saitama)
- Fiscal 2015
- Takino Plant (Kato, Hyogo)
- Fiscal 2015
- Fukuoka Plant (Koga, Fukuoka)
- Fiscal 2020
- Gunma Central Plant (Ora, Gunma)
- Fiscal 2021
- Shiga Plant (Higashiomi, Shiga)
Overseas Group Sites
- Fiscal 2017
- Siam Toppan Packaging (Thailand)
- Fiscal 2017
- Toppan Leefung Dongguan Plant (PRC)
TOPIC
Good Risk Sense Awards for 2023
On July 15, 2023, Toppan Inc. won a Chemical Daily Award and Risk Sensitivity Study Group Award at the FY2023 Good Risk Sense Award ceremony sponsored by the Risk Sensitivity Study Group* of Japan. Toppan Inc. was selected in recognition of the outstanding performance of Anzen Dojo and other safety initiatives in heightening safety awareness and reducing the risk of occupational accidents.
- *
- Established by the Japan Society for Safety Engineering under the Science Council of Japan. The group monitors corporate safety activities and commends outstanding initiatives to make them visible to other Japan-based companies.
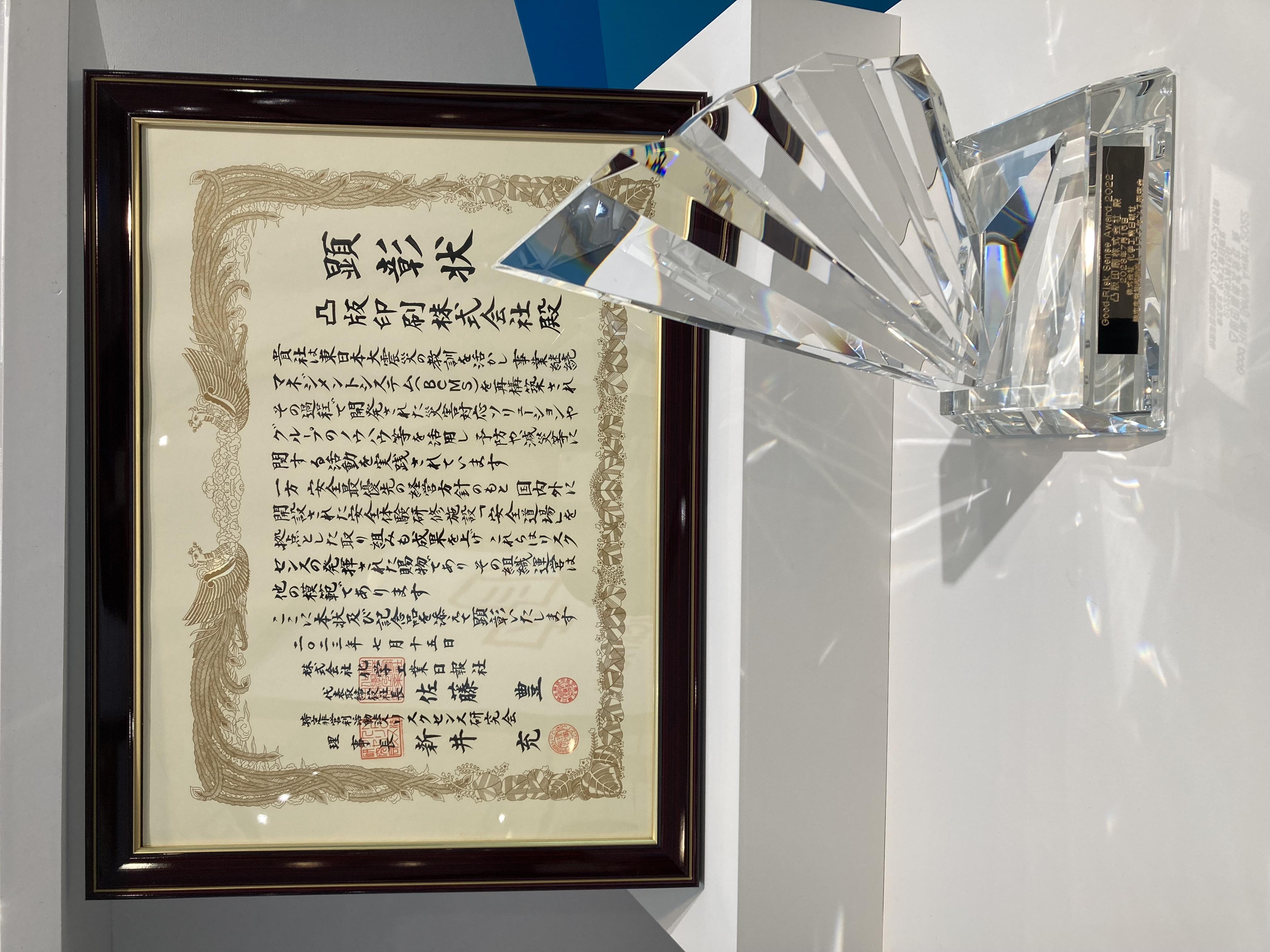
Enhancing Employee Safety Awareness
A Safety Project has been formed at TOPPAN Holdings Inc. with members from the Personnel & Labor Relations Division and the Manufacturing Management Division. Project members regularly visit Group sites to monitor their safety activities and carry out onsite patrols with a view to reducing the risk of occupational accidents at production sites across the Group.
To bolster defenses against COVID-19, TOPPAN site members across Japan have taken part in a diverse series of remote meetings focused on the implementation of safety education and the standardization of safer work procedures for personnel working at production departments throughout the Group. Basic online training sessions have been provided primarily for safety masters and employees in charge of safety across Japan. Site personnel have also gathered at subcommittees to deliberate safety measures in their production processes. In parallel with these ongoing remote initiatives launched during the pandemic period, we have also resumed onsite, in-person safety meetings and training sessions in conjunction with the onsite inspections to promote safety activities throughout TOPPAN.
Enhancing Employee Health with the Health Insurance Union
We engage in a “collaborative healthcare” initiative encompassing health improvement activities, in cooperation with the TOPPAN Group Health Insurance Union. Healthcare promotion committee members deployed across operational sites and 51 clinics supporting employee health throughout Japan collaborate with the health insurance union to develop measures for maintaining and enhancing the health of Group employees. The health insurance union and Group sites leverage their own resources and strengths to implement their health promotion activities in a solid alliance. Their current initiatives include measures to increase family health checkup rates and forest therapy sessions that bring individual employees and Group organizations into natural surroundings to enhance their vitality.
Data on Occupational Accidents
Under the “safety first” principle, TOPPAN is creating safe, secure workplaces towards the elimination of occupational accidents throughout the entire Group.
Data
2019 | 2020 | 2021 | 2022 | 2023 | ||
---|---|---|---|---|---|---|
Deaths from occupational accidents | TOPPAN Inc. | 0 | 0 | 0 | 1 | 0 |
TOPPAN Inc. and some of its subsidiaries*3 | 0 | 0 | 0 | 1 | 0 | |
Frequency rate*1 | TOPPAN Inc. | 0.144 | 0.095 | 0.046 | 0.092 | 0.000 |
TOPPAN Inc. and some of its subsidiaries*3 | 0.342 | 0.238 | 0.444 | 0.340 | 0.139 | |
Severity rate*2 | TOPPAN Inc. | 0.003 | 0.001 | 0.001 | 0.345 | 0.000 |
TOPPAN Inc. and some of its subsidiaries*3 | 0.007 | 0.004 | 0.014 | 0.169 | 0.003 |
Fiscal 2023 Results
Fiscal 2023 | Deaths from Occupational Accidents | Frequency Rate*1 | Severity Rate*2 |
---|---|---|---|
TOPPAN Inc. | 0 | 0.000 | 0.000 |
Some of its subsidiaries*3 | 0 | 0.290 | 0.006 |
Subtotal | 0 | 0.139 | 0.003 |
Group companies in Japan*4 | 0 | 0.184 | 0.002 |
Group companies overseas*5 | 0 | 2.380 | 0.022 |
Total | 0 | 1.014 | 0.010 |
Notes
- *
- Period covered: January 1–December 31
- *1
- Number of occupational accidents requiring employee leave, per million cumulative actual working hours (reflects the frequency of occupational accidents)
- *2
- Number of workdays lost as a consequence of occupational accidents, per thousand cumulative actual working hours (reflects the severity of occupational accidents)
- *3
- Fiscal 2022: 30 domestic subsidiaries under the control of either Toppan Inc**. or its business divisions
Fiscal 2023: 13 domestic subsidiaries under the control of either TOPPAN Inc**. or its business divisions
The results for TOPPAN Inc. pertain to its employees, including those consigned to other companies within the Group. The personnel structure of TOPPAN Inc. is unchanged from that of the former Toppan Inc. - *4
- Fiscal 2022: Toppan Inc. and 30 Group companies in Japan
Fiscal 2023: 46 Group companies in Japan - *5
- Entities covered: 101 Group companies overseas
- *
- Change in aggregate classification: Some of the entities covered in aggregate have been reclassified with the transition to a holding company structure. With other pertinent data, subsidiaries under the control of the head office are reclassified as “Group companies in Japan.” (These subsidiaries were formerly classified as “some of its subsidiaries” under the control of the former Toppan Inc**. until fiscal 2022.) The current reclassification aims to align fiscal 2023 data with the data up to fiscal 2022, as the former head office functions of Toppan Inc. have been transferred to TOPPAN Holdings Inc.
- **
- Only “T” is capitalized in “Toppan Inc.,” the entity before the transition, to distinguish it from TOPPAN Inc. (“TOPPAN” in all uppercase), one of our current operating companies.
Measures for Mental HealthcareBack to Top
TOPPAN works with industrial physicians and the health insurance union to prevent mental health problems at the workplace. The measures taken broadly adopt “primary, secondary, and tertiary prevention” strategies, as well as prevention-focused approaches (“fundamental prevention”) to improving communication skills and enhancing physical and mental health through better sleep. Diverse knowledge and expertise from outside of the Group have enabled us to develop in-house training programs and materials attuned to our internal mental healthcare needs. The training programs at TOPPAN embrace theories and methods such as cognitive behavior therapy, clinical art therapy (via the Art Salon workshop), the five factors & stress (FFS) theory, and Adler’s theories of individual psychology, as well as front-line findings on physical and mental conditions. Training for new employees, rank-based training, division-based training, workshops at workplaces, and training for candidates for overseas assignments all play important roles. Emerging challenges such as harassment prevention and special care for remote working are comprehensively addressed in our training regime. When individual employees are absent from work for mental health reasons, we support their recovery step by step by encouraging them to concentrate on their own medical treatment, preparing them for their return to work in advance, confirming their readiness to return, and extending support when they are back at work. Deliberative support helps employees maintain good balance between work and medical treatment and avoid any exacerbation or recurrence of mental burdens.
Developing a 3D Stress Check & Support
TOPPAN has analyzed extensive data from employee stress checks and from specialists overseeing mental health problems at the workplace. The risk factors for mental illness identified include not only typical excessive stress, but also physical and mental conditions linked to unhealthy lifestyles and major changes in personal and working environments. Based on these findings, we have developed a proprietary 3D Stress Check & Support system that offers detailed risk assessments and automatically prescribes tailored mental hygiene support through video coaching programs that employees in need can access anonymously. Stress checks are also arranged twice a year for graduates hired in the last 24 months, redoubling our mental healthcare support for new hires. A question to measure presenteeism has been assessed in our stress checks since fiscal 2022 (single-item presenteeism question [SPQ], University of Tokyo), and new questions to measure absenteeism have been introduced in fiscal 2024. These questions clarify how the mental/physical conditions of employees relate to their productivity. Meanwhile, feedback on the group analyses performed using data from the 3D Stress Check & Support system is relayed to managerial staff to guide their efforts towards workplace improvements.
Overview of Mental Healthcare Activities
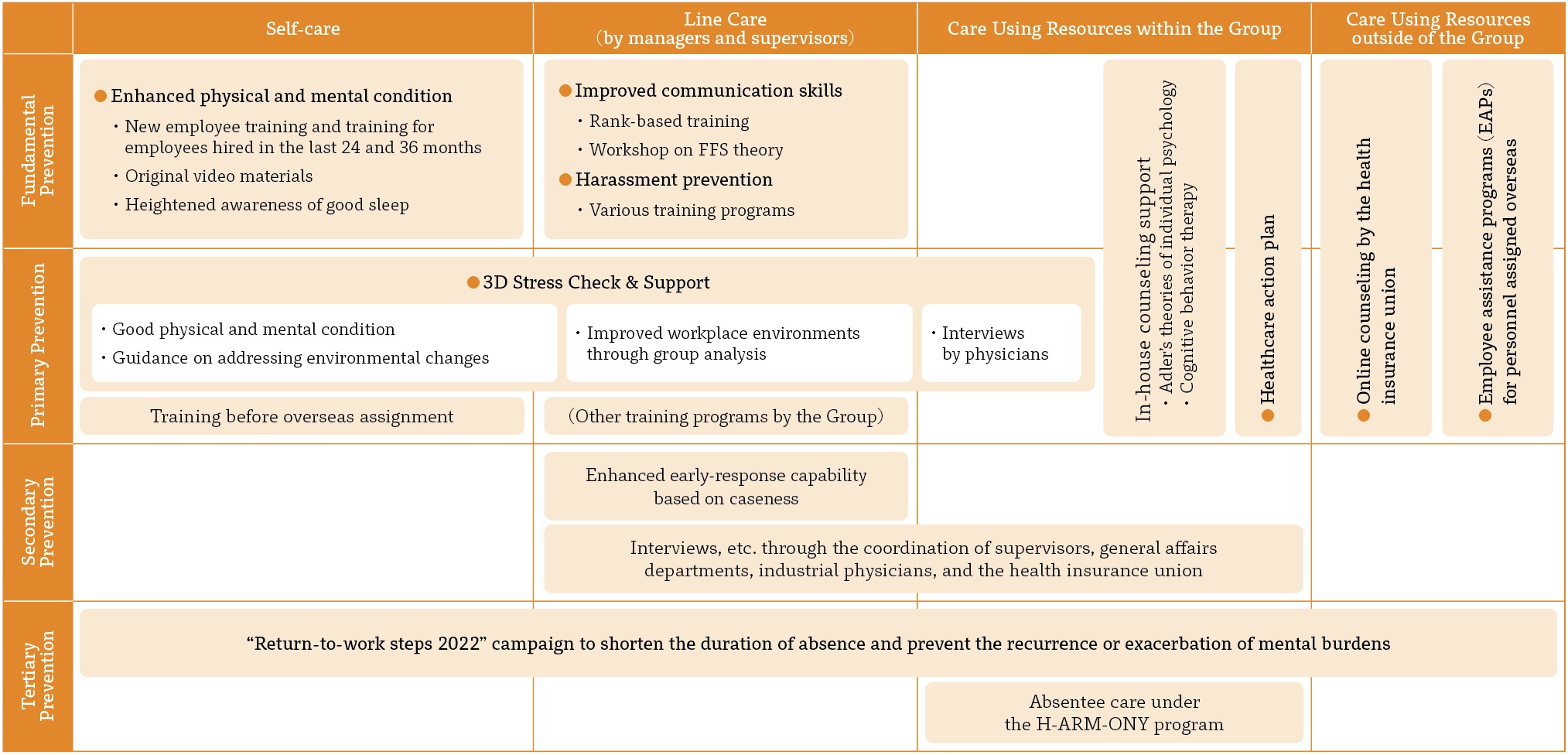
Presenteeism*
Fiscal 2022 Result | Fiscal 2023 Result | |
---|---|---|
Measuring method | SPQ-incorporated stress check | SPQ-incorporated stress check |
Result | 81.1% | 80.0% |
- *
- An indicator proposed by the World Health Organization (WHO) to measure performance deficits due to health problems. Presenteeism is productivity loss resulting from the health problems of employees while they work. Absenteeism is absence from work for health reasons (sick leave). Presenteeism tends to be overlooked in attendance management systems.
Work StylesBack to Top
Labor representatives and management at TOPPAN Inc. have been engaged in a vigorous dialogue since 2019 to devise flexible work styles. A remote work system adopted on October 1, 2020 covers working from home, working from satellite offices, and mobile working. A smart work system launched in 2018 spurs innovation by achieving full-time work from home on a discretionary basis. We have also revised existing working arrangements and introduced new systems to adapt to post-pandemic, new-normal work styles. Eligibility requirements for remote and smart work systems were relaxed in 2023, and employees are now given the discretion to choose four-day work weeks. Beyond system improvements, ongoing training programs encourage employees to establish their own work styles in the new-normal environment. Employees learn to set individual goals, commit themselves to incremental tasks towards their goals, and actively collaborate with diverse people inside and outside of the Group.
Supporting Work-Life Balance
At ongoing business councils and labor-management committees to support work-life balance, labor representatives and management exchange opinions and deliberate measures to further shorten overtime working-hours and comply with the revised Labor Standards Act of Japan. They also analyze actual overtime practices, review recently adopted working systems, and deliberate the introduction of new systems. Labor and management at each operational site discuss tailored approaches to creating an accommodating environment where employees are encouraged to take leave. The target paid leave set is at least 10 days per year per employee. Employees working for TOPPAN for 30 consecutive years receive a reward and a period of leave.
Annual Paid Leave Used (TOPPAN Inc.)
Fiscal 2019 | Fiscal 2020 | Fiscal 2021 | Fiscal 2022 | Fiscal 2023 | |
---|---|---|---|---|---|
Average paid leave used (days) | 11.1 | 10.3 | 10.5 | 11.9 | 11.7 |
Average ratio* | 60.6% | 55.2% | 57.0% | 64.6% | 64.3% |
- *
- Average ratio = average paid leave used / average paid leave granted
Monthly Overtime Working (regular employees, TOPPAN Inc.)
Fiscal 2021 | Fiscal 2022 | Fiscal 2023 | |
---|---|---|---|
Average monthly overtime hours | 20.87 | 21.68 | 22.08 |
Achieving a Good Work-Life Balance
Various systems and measures are in place to balance work and life for employees and their families: worksite cafeterias and sports facilities, dormitories for single employees, and resort facilities at offsite locations; a financing system to encourage savings; asset-building support through stock ownership and collective insurance; enhanced systems for maintaining good work-care balance for employees with children and nursing care responsibilities; sick leave and extended leave; retirement benefits and corporate pension; and enriched systems for living support. The TOPPAN Group Fraternal Benefit Society* runs welfare programs for leisure, health promotion, and life design support. On the diversity front, our benefit systems for spousal arrangements have accommodated same-sex partners and common-law marriage since July 2020, facilitating celebration and condolence leave and benefits such as allowances and wedding gifts.
- *
- TOPPAN Group Fraternal Benefit Society
Founded by employees and TOPPAN under the philosophy of co-creation through mutual support. The society’s welfare programs help employees and their families maintain secure lives.
Announcing an Action Plan for Childcare Support
TOPPAN Inc. publishes a “common employer’s action plan” based on an applicable Japanese act*. The plan aims to develop a working environment that supports balanced work and family life for employees with young children. Employers are expected to design their own plans in order to flexibly arrange working conditions for diverse employees, including those not raising children.
- *
- Act on Advancement of Measures to Support Raising Next-Generation Children
Housing for Single Employees
TOPPAN is updating the housing for single employees in the Group. Our dormitory is set within a contemporary residential environment that has been developed to improve the work-life balance of employees by shortening their commutes to the main operational sites and providing a secure, comfortable living climate. The dormitory is equipped with TOPPAN décor products designed for comfortable living. A soundproofed theater and common lounge facilitate communication among residents.
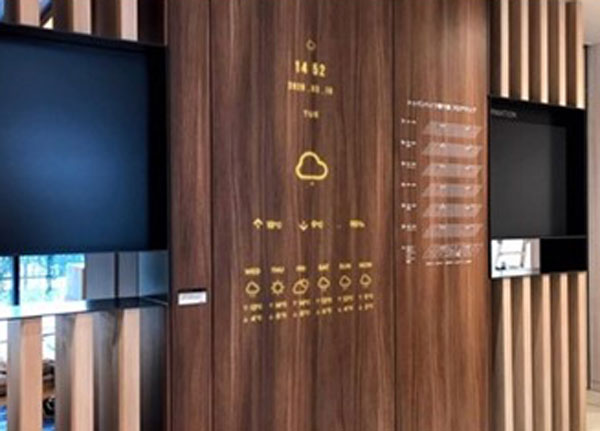
TOPPAN décor products
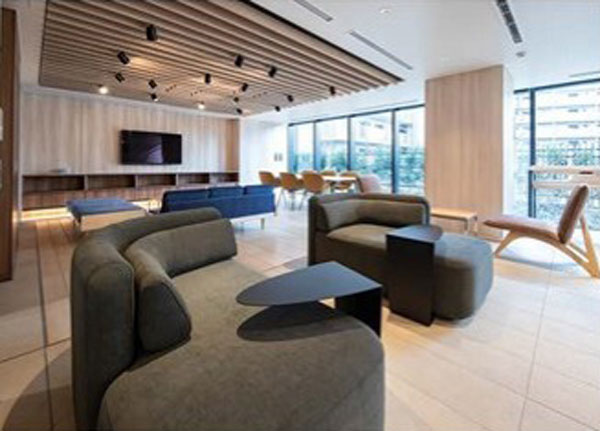
Lounge
Main Leave Systems and Family Benefits
Leave Systems, Family Benefits, and Work-Life/Next-generation Support Measures
Stock Leave | Annual paid leave left unused for two years after being granted can be accumulated, up to a ceiling of 50 days. It can be used for reasons such as medical treatment for employees or their spouses, healthcare or nursing care for employee families, fertility treatment, recovery-work after disasters, or school closures due to circumstances such as infectious diseases or natural disasters. (To be taken in half-day allotments, as needed.) |
---|---|
Childcare Leave |
Parents can take leave consecutively until their child reaches two years of age. The first five days taken are paid. From day six, employees receive 15% of their regular salaries (until the child’s second birthday) and a 1,000-yen daily subsidy from the TOPPAN Group Fraternal Benefit Society. They can also work for shorter hours (up to two hours reduced per day) or select a flextime or irregular working schedule, until their child completes the fourth year of elementary school. TOPPAN subsidizes certain childcare costs and operates a related consultation desk. A leave system for newborn care was also introduced in October 2022 under the amended Child and Family Care Leave Act of Japan. Regardless of gender or length of service, an employee can take up to four consecutive weeks of leave within eight weeks from the child’s birthday or expected delivery date, whichever is later. The 28 days can be split into two periods, if desired. |
Rehiring of Employees who Leave the Company to Raise Children | Rehiring is guaranteed for an employee who resigns to deliver and raise a child, provided that the employee has worked for TOPPAN for more than three consecutive years up to the date of resignation. A resigned employee who meets this condition will remain eligible for rehiring until May 1 of the year when the child enters elementary school. |
Nursing Care Leave | For every family member requiring care, an employee is entitled to one year of consecutive or aggregated leave and up to three years of other work-hour adjustments (e.g., staggered working hours, two-hour daily reductions). The TOPPAN Group Fraternal Benefit Society pays a 1,000-yen daily subsidy during the leave. TOPPAN offers nursing care information and contracts external guidance counselors. |
Leave for Child Healthcare | Employees can take up to 10 days of leave a year, regardless of the number of children they are raising. (To be taken in half-day or one-hour allotments, as necessary.) |
Volunteer Leave | Employees can engage in socially beneficial activities for up to one year on leave with an allowance. |
Staggered Work-hours | An employee can adjust daily working hours upward or downward by one hour to avoid rush-hour commutes during pregnancy and by two hours for childcare (until their child completes the fourth year of elementary school). |
Dependent Family Allowance | For employees with children, TOPPAN pays a monthly allowance of 20,000 yen for each child. This allowance is discontinued on the first April 1 to arrive after the child’s 20th birthday. (No limit for the number of children is applied.) |
Partial Subsidization of Babysitter Expenses | The TOPPAN Group Fraternal Benefit Society subsidizes 50% of babysitter expenses (up to 5,000 yen per day) for up to 90 days a year. |
Guidance on Finding Kindergartens and Daycare | Specialists provide knowledge and skills to parent employees seeking kindergartens and daycare for their children, as practical guidance to help them return to work from childcare leave more seamlessly. |
Other | The TOPPAN Group Health Insurance Union covers standard medical costs for childbirth. The union also sends parent employees a complimentary childrearing magazine. |
TOPPAN Job-based Personnel System
TOPPAN is reforming various personnel systems to better reward human assets with diverse skills and career backgrounds by promoting their skill and career development, assigning important roles to younger employees, enabling veteran employees to demonstrate their accumulated skills, and creating a working environment where every person can take on new challenges. Our newly restructured personnel evaluation system grades employees not uniformly by position, but granularly by incorporating job-specific elements. An employee’s tenure, or years in a position, is no longer an evaluation metric. New personnel evaluation metrics—“the creation of a sustainable society,” “diversity,” “respect for human rights,” and “social value creation”—have been added to our basic grading system to help guide employees through the processes of behavioral innovation and personal growth towards enhanced organizational performance throughout the Group. The personnel systems of TOPPAN Holdings Inc., TOPPAN Inc., TOPPAN Edge Inc., and TOPPAN Digital Inc. are being integrated following the transition to a holding company structure in October 2023. This will increase the mobility of human assets within the Group to maximize synergies for enhanced corporate value.
Second-job and Side-business Arrangements
TOPPAN Group employees can engage in second jobs or side businesses, as a basic rule, provided that they can avoid prolonged work in their dual jobs and fulfill the duties of security, confidentiality, non-competition, and good faith in their work at TOPPAN. Ninety-two employees used these arrangements at TOPPAN Inc. in fiscal 2023 (52 employees in fiscal 2022).
Offices Suitable for Diverse Work Styles
Our office environments have been adapted to a diversity of new and flexible work styles that facilitate innovation. Along with shared offices in-house, TOPPAN has opened “Atte,” an office where innovation is spurred through face-to-face meetings under the new-normal circumstances. We have also set up “ICT KŌBŌ” studios across Japan as bases for our system development activities driving DX business. Nationwide studios will encourage human assets to choose diverse ways of working as remote workers with shortened commuting times, create new businesses through interactions with local people and companies, and activate communities through increased local employment.
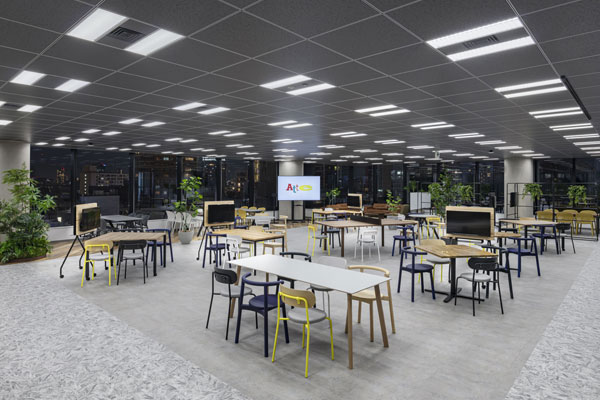
Atte
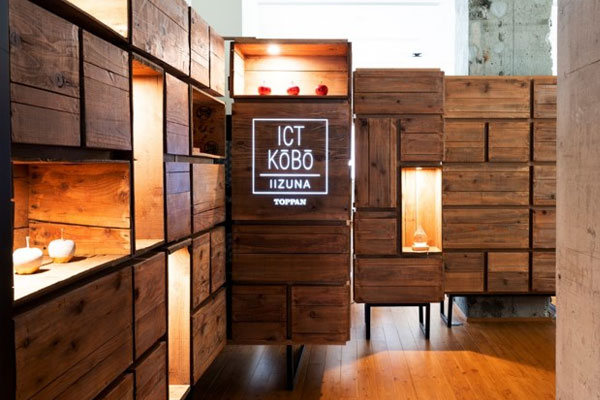
ICT KŌBŌ